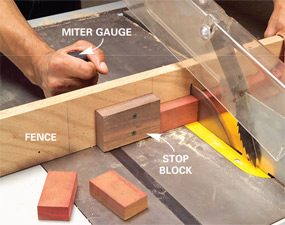
It can be difficult to transport rough lumber in your car. Take your handsaw and tape measure along with you to the shop. Additional boards can be purchased in case the one you have bought doesn't fit. Make sure you have the right knots and checks on your board. Otherwise, they might not fit as well as you would like. You don't want a board that is too small and has to be cut up again. This is a wasteful way to spend your time and money.
Minimal wastage
A sawmill can turn 59% to 50% of rough lumber into boards by cutting it. The remainder of the log, which includes sawdust or bark, is considered waste. The log should be cut to a smaller size, but not more than 20%. Here's an easy formula to calculate how much wood is left over after a board has been cut. To achieve the desired lumber thickness and length, the sawmill should take out 18% of the board's volume for a nominal 4 foot board.
For one thing, rough lumber rarely comes in uniform dimensions. The dimensions of hardwood that you purchase from a big box retailer are often known. This allows for you to plan your project using the standard size. The rough edges of lumber can be uneven, which leads to wasted material. Additionally, rough-cut lumber often requires a common width which results in a lot wasted lumber. Furthermore, this waste can't ever be reused.

Preparation
Measure the length of your material before you start cutting rough lumber. Rough lumber may not arrive at the lumber yard perfectly flat. It may also not have parallel faces and edges, and may require several passes to flatten. A good rule of thumb is to remove 1/16" per pass. If your lumber has concave surfaces you should run it through the saw keeping the concave surface in place.
It is recommended that rough-cut lumber be flattened until it is 1/4 inch thick before being cut. After flattening the face, plane to the thickness of the finished board. Once you know the thickness of the rough lumber measure the finished length and width. Be aware of any imperfections and plan accordingly. Be sure to leave a minimum of one-quarter inch space on each side of the board. You can also plan your project using the available boards. Do not buy lumber that is uneven. It will be difficult to work on boards that are bowed, warped or twisted.
Prices
There are two types. Dimensional lumber and rough-sawn. Home improvement shops usually sell finished lumber but only rarely rough-sawn. Both types of lumber are typically carried by local sawmills or lumber yards. The only difference between these two types lies in the work involved. Because it is less processed, rough-sawn boards can be more economical. It is also wider and thinner than finished lumber.
While purchasing lumber from a mill/lumber yard is usually cheaper, it is less likely that the lumber will be available in standard lengths. Making your own lumber can save you money over buying rough-sawn lumber. However it will require some space and additional power. It can also be noisy and requires some training. Consider the local zoning laws if you intend to use your mill.
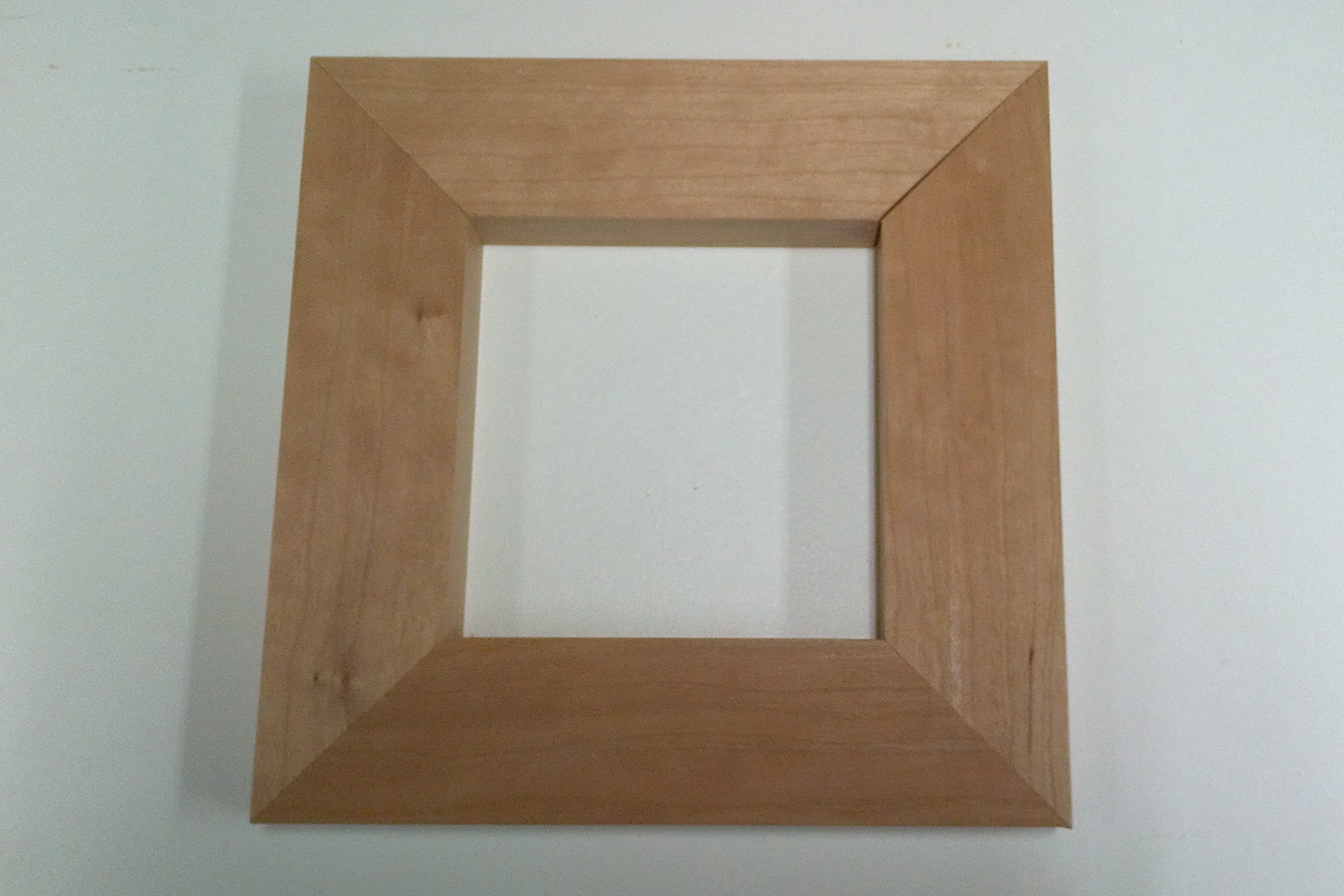
Source
There are many options for lumber purchases. There are different sizes, shapes, cuts, and finishes to choose from. Rough sawn lumber, for example, is unsanded and unfinished lumber that has been cut into planks. This type of lumber is more durable than others because it contains more moisture. It's also thicker and stronger than surfaced wood. The following are some benefits of using rough sawn lumber for your woodworking projects.
Its availability and low cost are its main pros. Rough lumber does not need to be treated and cannot usually be purchased at a hardware shop. However, this type lumber comes with its own pros and cons. It is generally cheaper by volume, but costs more per board foot to transport. Plus, it takes more time to finish than treated wood. When deciding how many lumber to buy, this is an option you may want to consider. You might consider buying a lot of rough sawn lumber to finish your project.
FAQ
What is the difference of plywood and particleboard?
Plywood can be described as a mixture of layers and wood that have been pressed together with pressure. Plywood is available in a variety of thicknesses. It is often used to make cabinets or flooring. Particle board consists of sawdust mixed and resin. The resin is then compressed into large blocks. It's commonly used for home improvement projects. Both boards are strong and can be easily cut.
What would be your first step in woodworking?
You can start with softwoods like pine or poplar. After you are comfortable with the softwoods, move to hardwood.
Can this be a way to make money?
Yes! Many woodworkers are already doing so. According to the U.S. Bureau of Labor Statistics' (BLS), in May 2012 the median annual wage of woodworkers was $34,000 This is more than the national average of 31,000 per annum.
Can I refinish my own furniture?
Yes! You don't have to hire a professional to refinish furniture. There are many ways you can do it yourself. Here are a few suggestions:
To remove stains and scratches, use sandpaper. After that, use a clean towel to wipe the surface.
Clear polyurethane varnish should be applied. Let dry completely before moving furniture around.
Use acrylic paint to paint furniture.
Stain can be used instead of paint. The furniture will get a rich look with the stain.
Apply shellac wax. You can protect your wood with wax and give it shine.
Statistics
- The U.S. Bureau of Labor Statistics (BLS) estimates that the number of jobs for woodworkers will decline by 4% between 2019 and 2029. (indeed.com)
- Overall employment of woodworkers is projected to grow 8 percent from 2020 to 2030, about as fast as the average for all occupations. (bls.gov)
- If your lumber isn't as dry as you would like when you purchase it (over 22% in Glen Huey's opinion…probably over 10-15% in my opinion), then it's a good idea to let it acclimate to your workshop for a couple of weeks. (woodandshop.com)
- In 2014, there were just over 237,000 jobs for all woodworkers, with other wood product manufacturing employing 23 percent; wood kitchen cabinets and countertop manufacturing employing 21 percent. (theartcareerproject.com)
External Links
How To
Tips for driving a nail in wood
First, choose the right size and type of tool to drive a nail through wood. The most common types of hammers are claw hammers, sledgehammers, mallets, ball peen hammers, and hatchets. Each kind of hammer has its own advantages and disadvantages. A claw hammer is best for hitting nails or hard objects. However, it can be difficult to pinpoint exactly where the blow will land. Although a sledgehammer can be used to hit large areas quickly, it is too heavy to be useful for small tasks.
Place your hand flat on the side of your chosen hammer so that the handle rests in your palm. Take the handle and hold it with both hands. But don't press down so hard you injure yourself. Hold the hammer straight up, keeping your wrist relaxed. Swing the hammer back towards the ground, with your aim at the middle of the nail. You should feel the impact of your hammer hitting the nail. If you're having trouble getting the hang of swinging a hammer, practice with a block of wood until you get the rhythm down.
Hold the hammer near your body until you're ready for the nail to be driven. Position the nail, so it's perpendicular to the surface of the wood. Keep your attention on the tip. Swing your hammer forward. Then follow through with the motions of the hammerhead. Repeat this action several times, gradually increasing the speed of the swing. When you are confident with the technique, add power to your swings. Hold the hammer high above your shoulders and pull it down. This way, you'll be able to put more energy behind your blows.
Once you have successfully drilled the first hole in the nail, remove the hammer. To remove the remainder of the nails, you can use a screwdriver/pry bar. To avoid splitting the wood, make sure the nail heads are not touching the board's surface.