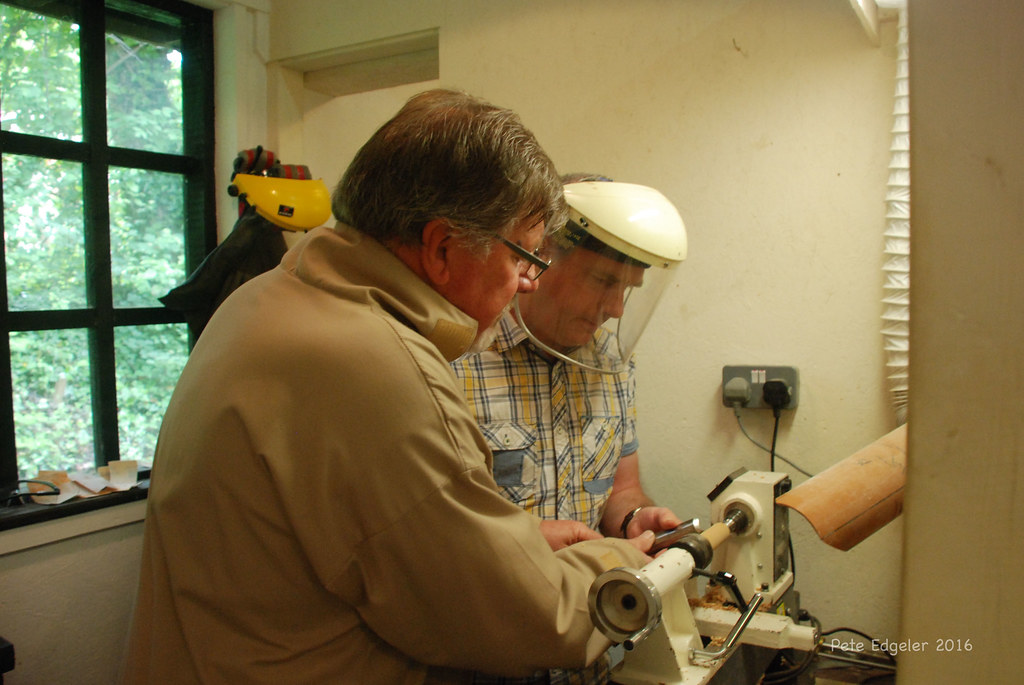
Philip Moulthrop began turning wood in 1979, learning his craft from his father, Ed Moulthrop. He works with a lathe and a chain saw to remove the green leaves from trees that are sourced from the southeast. After he finishes the bowl of the lathe, he refines it and then adds several coats of finishing. The entire process takes between four and one year. Once they're done, you can either buy the bowls or give them as gifts.
Philip Moulthrop
Phillip Moulthrop is known for his bowl made of red leopard maple. The process of wood turning, which he developed, has been a family tradition for three generations. In addition to their own creations, Philip Moulthrop's bowls are part of the permanent collections of several prominent museums and private collections around the world. Here are some of their most renowned pieces. For more information about this talented artist, read on.
The American artist Philip Moulthrop was born in 1947. He started his education in general arts when he was just 20 years old and quickly developed a passion for woodworking. At 16 he purchased his first lathe. He continued to expand his equipment. He was an innovator in his field, creating beautiful turned vessels that were well-received by the art community and the United States president. His work was soon recognized and he started selling his pieces at local craft fairs and galleries. He also began to receive international recognition.
Matt Moulthrop
The Matt Moulthrop bowls are a wonderful example of Georgia's rich woodturning tradition. The artist was born in Atlanta and received his BA and MBA from Georgia Tech. He worked for a few years in 9-to-5 jobs but never lost his love of woodturning. He was even recognized nationally for his bowls. His works are displayed at the ASU Art Museum, the Carter Center and the Racine Art Museum.
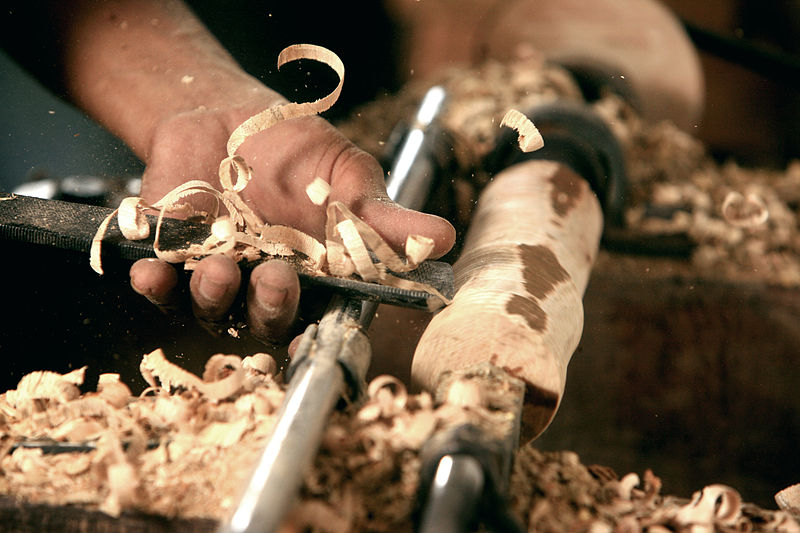
The Moulthrops have been recognized as world-class wood-turners, with works placed in prominent collections in the United States and abroad. Moulthrop pieces can be found in the Renwick Gallery of the National Museum of American Art. Collectors from all over the globe have taken to heart his bowls. During a Smithsonian photo shoot he signed every photographer a copy of his family's book.
Ed Moulthrop
Moulthrop was a bowl-turner in the early 1970s. He quickly earned a scholarship for Princeton University to study Architecture. Moulthrop spent a year in Vietnam and then resigned as an architect to pursue woodturning. His large-scale, hand-turned bowls have been recognized worldwide and are kept in prominent museums like the Museum of Arts and Design and the White House Collection of American Crafts. These bowls are made of domestic woods and polished to a clear finish.
The Ed Moulthrop wild cherry bowl measures nine inches wide by fourteen inches tall. These wood bowls can also be bought at Gump’s San Francisco. You can also see other Ed Moulthrop wooden bowls. Visit the exhibition to get a better idea of his work. He also creates a gorgeous catalog of his work. You can buy his bowls in museums but it is better to go to his studio and actually see it.
The Eagle & Phenix Dam Series
This limited edition series moulthrop bowls is made from wood from the Eagle & Phenix Dam. It's a series that was once located in Columbus, Georgia. The bowls have historical traces and were handcrafted in Atlanta by Philip and Matt Moulthrop. They are open for bidding during regular museum hours. Some bowls will be up for auction live.
The Moulthrop families has played a significant role in Georgia's development of wood-turned bowls. Three generations of Moulthrop have been turning bowls in Georgia for more than fifty decades. The museum is proud to display works from all three generations. Many of these pieces are highly prized for their large size and smooth, polished surfaces. His mosaic bowl technique, which involves glueing thin branches to a shaped bowl with thin branches, is featured in the exhibit.
Matt Moulthrop’s work
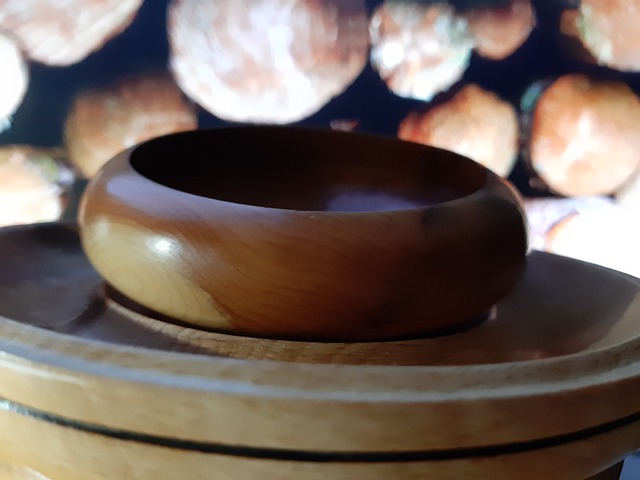
Matt Moulthrop was the son of Philip Moulthrop. He was taught by his father at an early age, and his passion for woodworking grew. Matt started his woodworking career after completing his BA degree at the University of Georgia. He also completed his MBA at Georgia Tech. He is now the third generation who makes wooden vessels. His work is displayed in many prominent art institutions such as the ASU Art Museum, Carter Center and the Carter Center. He is currently working on commemorative pieces for the Georgia Tech Alumni Association's 100th anniversary.
Georgia is not the only place he can turn wood. To find wood that is not common, he travels around the world. He creates unique pieces by turning trees from around the globe with tools and a hand-forged, lathe. His wood pieces are made from wood taken from both Southeast and exotic places such as underwater forests or volcanoes. If you are a fan of his work, be sure to check it out!
FAQ
How often should I buy new supplies?
Over time, you may need to replace your tools. If you're using hand tools, you'll need to sharpen them regularly. And if you're using power tools, you'll need replacement parts periodically. Try spreading your purchases over a few months so you don't buy too many at once.
What tools should you start with to become a woodworker
Woodworking is an art form that requires patience and practice. Learning how to use the various tools and techniques necessary for woodworking takes patience.
There are many different types of woodworking equipment available on the market today. Some prefer to use power tools and others prefer hand tools.
You have the freedom to choose what tool you want, but it is important that you select the right tool for your job. It may be a good idea to start with a basic set, if possible, if you don’t know much about hand tools.
You could also try learning how to use a router which is used to cut intricate shapes into wood. These tools can be purchased at most hardware stores.
Can I make my living doing this job?
Yes! Many woodworkers do. According to U.S. Bureau of Labor Statistics (BLS), woodworkers earned a median annual salary of $34,000 in May 2012. This is much higher than the national median of $31,000 per annum.
Do you know anything more about woodworking?
It is easy to underestimate how much work it takes to make furniture. Finding the right wood for the project is the hardest part. There are so many options for wood, it can be difficult choosing the right one.
Another issue is that wood does not have the same properties. Some woods will crack or warp with time. Others will split or crack. These are important considerations to make before you purchase wood.
Statistics
- The U.S. Bureau of Labor Statistics (BLS) estimates that the number of jobs for woodworkers will decline by 4% between 2019 and 2029. (indeed.com)
- Overall employment of woodworkers is projected to grow 8 percent from 2020 to 2030, about as fast as the average for all occupations. (bls.gov)
- If your lumber isn't as dry as you would like when you purchase it (over 22% in Glen Huey's opinion…probably over 10-15% in my opinion), then it's a good idea to let it acclimate to your workshop for a couple of weeks. (woodandshop.com)
- Average lumber prices rose about 600 percent between April 2020 and May 2021. (familyhandyman.com)
External Links
How To
How to stain hardwood
Staining wood is the process of applying chemicals to the wood's exterior, which alters its color. This chemical reaction causes wood to turn from whiteish to brownish. Although oak is the most popular type of wood to stain, there are many other types that can be used.
You can apply wood stains in many different ways. Some methods include mixing the stain along with a solvent like turpentine and then applying the mixture to the wood by brushing or spraying. You can also apply a solution containing water and dye directly to the wooden surface. The stain can be mixed with paints and varnishes to become part of the final coating.
Preparing your wood for staining is the first thing to do. The wood must be thoroughly cleaned to remove all grease and dirt. Sanding can smoothen out scratches and uneven spots. Next, you need to decide which stain you want. There are two basic kinds of stains: penetrating stains and non-penetrating stains. Penetrating stain penetrates deeper into wood than nonpenetrating, making them suitable for dark colors like mahogany. The best non-penetrating colors are those that work with light colors like maple.
After you've decided what type of stain to apply, get ready for your tools. Paintbrushes are great for applying stain because they allow you to evenly spread the liquid across the surface. To remove any stains left behind after painting, you will need some rags. If you plan to mix the stain yourself, make sure you have enough containers available to hold the different components of the mixture.
After you have prepared the materials, you can clean the area where you want to stain the wood. Clean the area with soap and warm water to get rid of dirt and grime. Use a dampened rag and clean water to wipe the furniture. If you intend to stain darker wood, make sure you get rid of any debris.
Next, spray the stain. Apply the stain by brushing or spraying it onto one side of the furniture. Slowly and carefully work your way along the grain to reach the opposite end. Be careful not to let the stain drip off the wood's edge. Let the stain dry completely before proceeding with the next steps.
A coat of clear polyurethane sealing agent is applied to protect the paint. Apply three coats of polyurethane sealer. Allow the third coat of polyurethane sealer to dry overnight before applying the final coat.