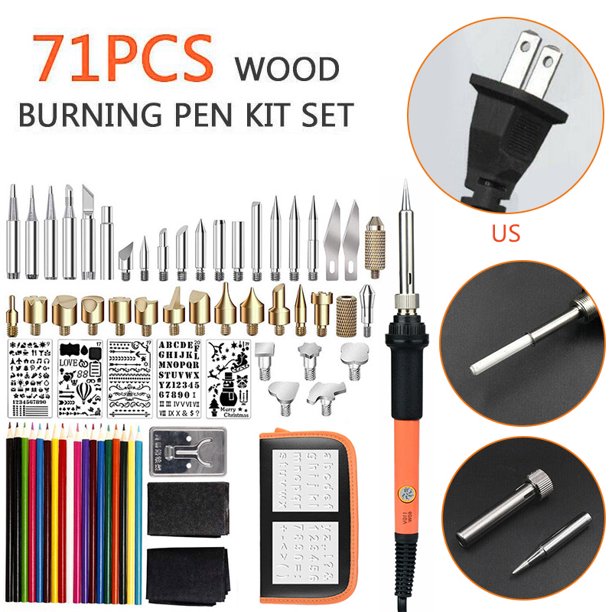
If you are looking to create beautiful and custom pieces for home, you might be interested learning more about pyrography. This ancient art involves the burning of intricate designs and ornaments into wood. It dates back to 17th century. The resultant burn marks make beautiful dark designs. This can include landscapes as well as portraits. This method is popular for home decor and has been used for centuries.
Yoko sugi ban
In 18th century Japan, a technique known as shou sugi ban is used to preserve wood by charring the surface. This process produces a rich charcoal black color on the wood's surface, and can also give it an alligator skin or cracked appearance. For a traditional, rustic look, the Japanese cedar is typically used, but other wood species may be used with varying degrees of success. The wood is protected against future damage by controlled charring, making it an excellent preservation technique.
Shau sugi ban
The only difference between shou, sugi ban sanding and traditional sanding lies in the way that char is removed. Shau sugi ban woodworkers scrape the charred top layer with wire brushes, while others use coarse sandpaper. Either way, you need to scrape enough char away to reveal the brownish-black color underneath. The resulting effect will be an alligator-skin-like pattern, and the sanding process is necessary to remove the excess char.
Shau sugi ban on cedar
Although the shou-sugi ban on all forms of pyrography makes for a beautiful wood finish, there are practical consequences. Not only can bits of charred wood be tracked throughout a building, but they can also be inhaled by people inside the treated space. This problem is being addressed by pyrographers who are now using a propane torch to lighten the fire instead of wood-burning. Here's a comparison of these styles.
Yakisugi ban on bassewood
The centuries-old Japanese technique of yakisugi ban (on cedar) can give wood beauty and strength. Shou sugiban is sometimes called this. It involves charring wood on the surface to make a beautiful pattern. The process is so popular in Japan that cedar is used in many shou sugi ban projects. Satoshi Kmura, operations director at a Japanese timber company, describes why shou shugi ban is so common and what it means to woodworkers.
Yaki sugi ban for blue stain pine
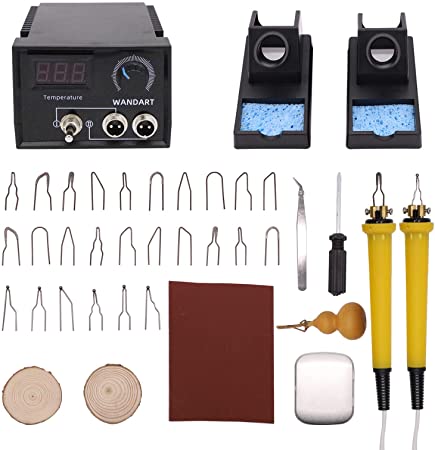
This process, commonly referred to as shou sugi ban, uses fire to preserve wood. For shou-sugi ban, cedar was traditionally used. However, other woods are possible. Although cedar has been used traditionally for this process however, yakisugi is also possible with other woods, such as maple, Ash, and Birch. This technique is very popular among traditional Japanese craftspeople.
Shau sugi ban on basswood
Charring cedar leaves it with a dark, rich color and distinctive crackled surfaces. Cedar is naturally water-resistant and repels pests. However, the charred surface has sculpting qualities. Untreated and reclaimed wood are available. To achieve a subtler, burnt look on a cedar panel, you can treat it.
Shau sugi ban on jelutong
Shou sugi ban is a prohibition on pyrography on wooden surfaces. There are many benefits. This technique improves the wood's natural patterns. Additionally, charred wood is more durable because of the thicker carbon layer. This is dependent on the timber species and environment in which the treatment is performed. Shou sugi ba is an environmentally friendly method to treat wood.
FAQ
What's the difference between a hobbyist and a professional woodworker?
Hobbyists are passionate about making things from wood, while professionals tend to be more focused on the quality and craftsmanship of their work. Hobbyists tend to take pride and share their creations with family and friends. Professionals will spend hours researching designs before they begin working on a project. They'll pay great attention to details, from choosing the most suitable materials to finishing the work perfectly.
How can I learn basic woodworking skills
You can start building furniture by making a bench. This project can be done with any kind of wood that you have at home. If you don't know what kind of wood to use, then go ahead and buy some cheap pine boards from Home Depot or Lowes. After building your bench, sand off any rough edges and apply a stain or varnish.
Is there a way to start my own woodworking company?
It can be difficult to start your woodworking business. There are many regulations and legal requirements that you will need to comply with. This doesn't necessarily mean that you should go through all the work of setting up a company. Many people join already-established businesses. You will only have to pay membership fees, taxes, and other charges.
How much should a woodworker charge per hour?
The hourly rate for a professional woodworker varies depending on many factors, including skill level, experience, availability, location, and other variables.
The average hourly rate for a skilled woodworker ranges from $20-$50 an hour.
A less experienced woodworker may charge as little as $10 an hour.
How do I choose the right tools for me?
It's important to consider your preferences and needs when buying tools. Do you prefer metal handles or plastic? What size screws or nails do you prefer? Do you prefer to use hand tools or power tools?
What else should I know about woodworking in general?
It is easy to underestimate the amount work involved with furniture construction. Finding the right wood for the project is the hardest part. It is difficult to choose between the various types of wood.
Another issue is that wood does not have the same properties. Some woods will warp over time, others will split or crack. You must take these things into consideration before purchasing wood.
Where can I find free woodworking plan?
Woodworking plans can be found online without the need to purchase books or magazines. You only need to Google search. Just enter "free woodworking" into the search bar, and you'll see hundreds of websites where you can download free plans.
Statistics
- Overall employment of woodworkers is projected to grow 8 percent from 2020 to 2030, about as fast as the average for all occupations. (bls.gov)
- The best-paid 10 percent make $76,000, while the lowest-paid 10 percent make $34,000. (zippia.com)
- The U.S. Bureau of Labor Statistics (BLS) estimates that the number of jobs for woodworkers will decline by 4% between 2019 and 2029. (indeed.com)
- Most woodworkers agree that lumber moisture needs to be under 10% for building furniture. (woodandshop.com)
External Links
How To
How do you measure wood accurately?
Wood measurement can be done using several methods. We use a digital scale (a tool for measuring distances), a laser-level (used to level your work surface), as well as a bubble level (used in order to level your work surface).
A digital caliper comes with two jaws. One jaw holds the object being measured and the other measures the distance between them. The digital caliper can be used to measure small distances such as the thickness of wood.
Laser levels are equipped with an infrared light beam, which projects a line across a floor. A red dot is created by the laser. It is possible to see if the surface of the surface are even by looking down at it. For large surfaces, laser levels are the best way to check their accuracy.
Bubble levels look similar to a compass. The device's center bubble is visible. The device will inform you if the surface is level if the bubble is in the center. Bubble levels are great for checking the accuracy and precision of smaller areas.