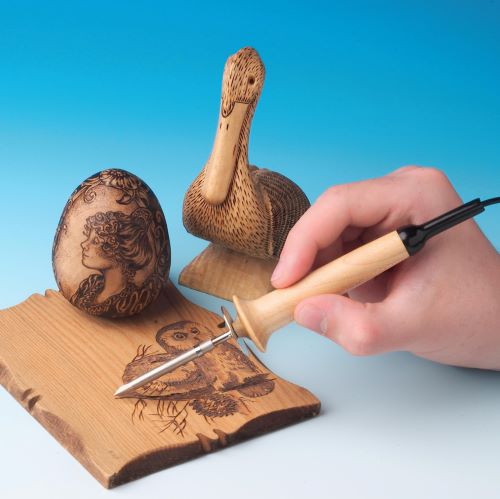
Beginner woodworking classes can be a great way to get started with a new hobby, and a great place to start is by learning the basics. Students can create simple projects that can be used in any room of the house. These small-scale projects are ideal for beginners and will help you gain the confidence you need in order to tackle more complex projects. The Shaker pegrack, small storage boxes, and wall-mounted bookshelves are just a few of the other planned projects.
Woodturning
You have many reasons to learn woodturning. The art of turning wood can be both therapeutic and beautiful. This is a way to return to the roots of wood and requires the use of your mind, hands and body. As it is an easy craft that doesn't require much machinery or tools, anyone can take a class. Michael Roper is a good instructor in woodturning and can help you learn the basics.
For an hour, classes cost $40 per person or $30 for a two-person class. The three-person class is a little more expensive, but you can always recruit a friend or family member. Hourly classes can be a great option for locals as well as those with restricted schedules or commitment issues. For three students, full-day classes cost upwards of $425. Three-person classes offer the best value if taken with two or more friends.
Bandsaw Box
The Bandsaw Box project is great for those taking woodworking classes. It's an excellent way to build safety with a bandsaw. This class is taught by Tom Wilson, a retired Industrial Arts teacher who has been teaching woodworking for over 30 years. He's also a builder of many student-built saw boxes. For this project you will need a 6” blank and some cardstock.
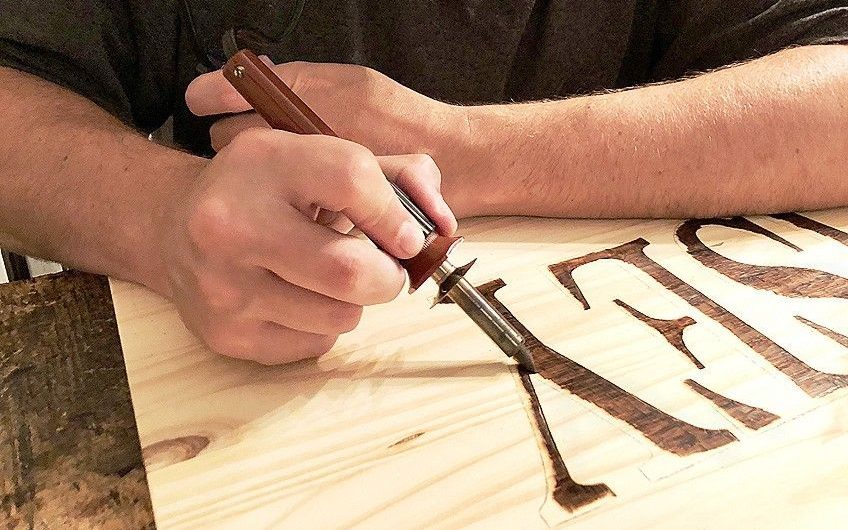
Before you begin cutting, mark the grain with a pencil and mark a line that follows it. After you have found the grain, move straight up towards the box. Next, turn the carcass in the opposite direction. You won't end with large pieces of wood on the one side. You'll then have a round box that is easy to stack and store away.
Bandsaw Spindle
Many woodworkers have little or no understanding of how to properly set up their bandsaw. They might not know how to align their blades or how to correctly set the guide block and thrust bearing. All of these aspects have a cumulative effect on the performance of a bandsaw. Wide bandsaw blades are best for smooth cuts. A large blade can cut through thicker material more easily. The blade's number of teeth also influences the quality and efficiency of cuts. The finer a cut will be, the more tooth count on the bandsaw blade.
Bandsaw blades are available in many thicknesses. The more thick the band, the straighter and stronger the cut will be. Thicker bands are more susceptible to cracking and breaking due to stress cracking. The result is a bigger bandsaw wheel. The ideal thickness of the blade is between 4 and 6 inches. Use a blade holder or a strop to adjust the direction of the cuts.
Hand carved bowls
It can be difficult to hand carve bowls from wood in classes. However, if your take the time learn about the materials and tools as well as the woodworking body you will be able make beautiful bowls that you can enjoy for many years. The author of this book, Ron Pickens, is a retired educator who grew up in Pickens, South Carolina. He holds a BA degree in Social Studies from Wofford College, and a MAT certificate from Converse College. He was a member of the United States Army from 1969-1971 and retired from Pickens High School, in 1999. Ron is a woodworker and enjoys teaching carving classes at Holly Springs Center.
Students will learn the basics of wood carving and how to use traditional wooden bowl carving hand tools to carve a wide variety of designs. The shape and purpose of a bowl are directly related to how the techniques and tools used for hand carving work. This traditional Scandinavian tradition can be seen in the simplicity of hand-crafted bowls. After the class, students will have a piece of great handiwork to proudly display at their dining room tables.
Masterclasses on Woodworking

You should take woodcraft masterclasses if you want to learn the art of woodworking. Woodcraft 101 offers many classes that will teach you how to create simple furniture or intricate carvings. Each class can be purchased individually or as part of a monthly subscription that costs eight dollars. A lot of the courses teach shop essentials like how to use a router tip, how to mill lumber and how you can use a table saw or jointer. Additionally, woodcraft masterclasses cover decorative inlay methods.
Paul Sellers’ courses on woodworking are available at the Woodworking Masterclasses web site. These videos provide a way to learn specific techniques and tackle difficult projects. You will need to pay $15 per month for access to the videos. Although the website looks great, there is no review or comment section. Although this is a significant problem, it's possible to request a free trial or trial to determine if the service suits your needs.
Brooklyn Woods
Brooklyn Woods offers a seven-week course that will teach New Yorkers a valuable new skill. This nonprofit has been around for 12 years and offers woodworking classes in New York to the jobless. Its students have little education, spotty work history, and many are former incarcerated individuals. Scott Peltzer, a former cabinetmaker who teaches the courses from the nonprofit's Gowanus offices.
The training program is completely free. Applicants must be interested in a career as a woodworker. The training is hands-on and includes instruction. Students are encouraged to form a sense of community through the program. Many students develop lasting relationships while others gain valuable life skills and substantial wages. It is a win-win program for everyone. Brooklyn Woods students are able to buy their dream homes. New Yorkers are also more employable thanks to the program.
FAQ
How do I calculate woodworking prices
The most important thing to remember when calculating costs for any project is to keep them as low as possible. You should always try to make sure that you are getting the best deal on materials. You should also consider other factors that could impact the cost of your project, such as experience, skill level, time, and money. If you want to get an idea of what you can expect to spend on different types of woodwork projects, check out our guide to the average price of common household DIY tasks.
How much should a hobbyist invest to get started?
If you're looking to start your own woodworking business, you'll probably need some capital to buy the necessary tools and supplies. A good place to start would be by buying a small table saw, drill press, circular saw, jigsaw, and sanding machine. These items aren’t too expensive so you won’t have to break the bank.
Which woods are good to use for furniture-making?
Woods are classified based on their hardness. Softwoods include cedar, pine, cedar, and Cypress. Because they are resistant, they can be used for outdoor furniture. Hardwoods include oak, maple, mahogany, and teak. They are generally indoors as they don't weather well outside.
Statistics
- The U.S. Bureau of Labor Statistics (BLS) estimates that the number of jobs for woodworkers will decline by 4% between 2019 and 2029. (indeed.com)
- Woodworkers on the lower end of that spectrum, the bottom 10% to be exact, make roughly $24,000 a year, while the top 10% makes $108,000. (zippia.com)
- Overall employment of woodworkers is projected to grow 8 percent from 2020 to 2030, about as fast as the average for all occupations. (bls.gov)
- If your lumber isn't as dry as you would like when you purchase it (over 22% in Glen Huey's opinion…probably over 10-15% in my opinion), then it's a good idea to let it acclimate to your workshop for a couple of weeks. (woodandshop.com)
External Links
How To
How to stain hardwood
Stain wood is a process that involves applying chemicals to the surface of wood, which changes its color. This chemical reaction causes wood to turn from whiteish to brownish. While oak is the most widely used type of wood for staining purposes, other types of wood are also available.
There are many options for applying stains to wood surfaces. Some methods involve mixing the stain with a solvent (such as turpentine) and then brushing or spraying the mixture onto the wood. Others use a solution made up of water and dye, which is then applied directly onto the wood. Stains can also be mixed into paints and varnishes, becoming part of the finish coating.
The first step in staining wood is preparing the surface. You must clean the wood well to remove any grease or dirt that might interfere with the application of the stain. Sanding the wood removes scratches and imperfections. Next, you need to decide which stain you want. There are two main kinds of stains available: non-penetrating stains and penetrating. Penetrating stains penetrate deeper into the wood than non-penetrating ones, making them ideal for dark colors such as mahogany. The best non-penetrating colors are those that work with light colors like maple.
After deciding on the type of stain, you want to apply, prepare your tools. Paintbrushes are great for applying stain because they allow you to evenly spread the liquid across the surface. It is a good idea to have rags on hand in case you need them to clean up any stains that may remain after you have finished painting. If you intend to mix the stain yourself you will need enough containers to hold all the components.
Once you have prepared all your materials, it is time to clean the areas where you will stain the wood. Clean the area with soap and warm water to get rid of dirt and grime. Use a dampened sponge and warm water to clean the entire piece. You should remove any debris, especially if your plan is to stain darker wood.
Apply the stain next. The stain can be applied by spraying or brushing the stain onto one end of the furniture. Move slowly and carefully along the grain of your wood until you reach its opposite end. The stain should not drip off of the wood's edge. Before proceeding to the next step, let the stain dry thoroughly.
Apply a clear polyurethane sealant to protect the painted surface. Apply three coats of polyurethane sealer. Let the third coat dry overnight before you sand the final coat.