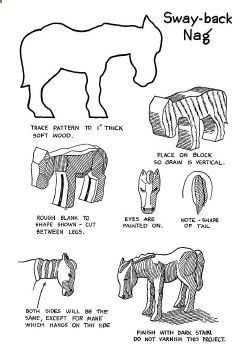
Step one in chip carving is to imagine where the blade should be. Then, cut the tile starting from the point, working your way up to progressively larger chips. Be careful not to pull the chips out but gently wiggle them. You can cut the tile a little deeper if bits are still attached to the tile. Repeat the process until the tile looks finished. You can then create your own unique chip carvings using a pattern.
Freeform style carving
In free form style chip carving, you can use a split blank and a sharp, straight-edged gouge to carve an image on the wood. Because its fibers have straight edges, the split blank lets you use more power when carving. You can also cut in either direction by flattening the top and removing it from the bottom. To improve your carving, experiment with different templates and create your own designs.
It can be difficult to carve, but once you learn the basics, the rewards will be well worth it. The creation of a design can take twice as long as the actual carving. Chip carving often involves many ridges or cuts. The "sharpness” at the bottoms can be crucial. Whether you carve a circle, the "sharpness" of the ridges is important.
Using angled cuts
An angled knife is used to carve a chip. You need to be aware of how it will look. Most likely, the chip will have two sides. One side will be straight. The knife's point should be at the intersection of these two walls. The third side should be cut at the lowest point.

Chip carving works well when the wood has a light color. This allows for greater contrast between the positive space and the negative. A lighter wood color will allow for greater contrast in shadows. Straight chips will highlight the negative space above them, while angled chips will create a subtle shadow that will appeal to the eye. The chip will look as though the letters are being cut from wood if it is angled.
Flexcut knives:
If you want to begin chip carving with an excellent, professional quality blade, you should consider investing in a Flexcut knife. These American-made knives are highly polished and come pre-sharpened. However, they need to be regularly stropped in Flexcut Gold polishing material. This knife's ideal bevel angle is 15 degrees. For chip carving, you should hold the knife at this angle.
If you're new to chip carving, you might be surprised by the versatility and accuracy of these knives. Every Flexcut knife has a reliable, long-lasting edge. The handles are made of ergonomically-shaped wood. The knives can be used to control each cut precisely and minimize chipping. Flexcut provides a special coating on your cutting tools that prevents chips by creating a protective layer.
Designing a pattern
To make a chip carving pattern, begin by drawing a design. This pattern can be simple or more complex, such as a circle, square, or oval. It is important that the lines are straight. It might take some practice before it becomes second nature. You can practice the technique by creating a scrap board. Once you have a design, you can start carving.
You can draw a grid to help you carve squares. This pattern allows you to create unique pieces by experimenting with different designs. You will need a pencil or ruler to draw the pattern. The grid should have each cell squared and the sides of each cell be 3/16" to 1/4". To make triangles you can connect each corner of a cell to another to create triangles.
Getting started
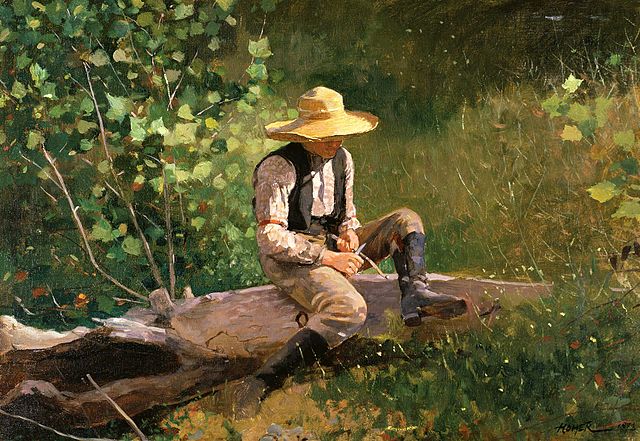
You can start chip carving by learning the basics. Most designs can be traced on graphite or paper. To ensure accuracy, you can use a ruler as you trace along each edge of the wood. To erase traced lines, you could also use a pencil or eraser. After you have perfected this technique, practice on a larger work surface until you get a firm grip.
Chip carving is very easy to learn and it doesn't cost a lot. Chip carving is far more simple than other wood carving skills. Chip carving can be used as an artistic outlet for creating beautiful pieces by beginning carvers. Personalize pieces to be given as gifts or used in your home. It is a rewarding hobby that can be passed down from generation to generation. A small piece of wood can be used to practice chip carving techniques, such as a wooden spoon.
FAQ
How can I learn basic woodworking skills
A great way to start learning how to build furniture is by building a simple bench for yourself. This project can easily be done using whatever wood you have at your house. You don't need to know which type of wood you should use. Instead, get some pine boards at Lowes or Home Depot. You'll need to sand the bench after it's built. Then, finish it with varnish or a stain.
Do you have any tips on starting a woodworking business?
It's not easy to start your own woodworking business. You won't mind working hard if your hobby is something you love. You will probably love the challenge of starting your own business.
When you are launching a new venture, it is important to be aware of the possibility that you will encounter unexpected difficulties. You may run out of money suddenly. You might find customers not willing to pay the amount you expected. You must be ready to deal with such situations in order to survive.
One tip is to have a separate banking account for your company. You will always know how much money you have coming in.
Can this be a way to make money?
Yes! Many woodworkers have this ability. According to the U.S. Bureau of Labor Statistics, the median annual woodworker wage was $34,000 in May 2012. This is significantly higher than the national average, which is $31,000 per year.
How can a woodworker start making money?
Many people learn how to make furniture in order to set up an online business. However, if you're just getting into furniture building, there are other options than selling on Etsy. You could sell at craft fairs or local events. A workshop could also be offered for people who are interested to learn how they can build their own furniture. You might be able to offer services like remodeling homes or making custom pieces for clients if you are a skilled carpenter.
Is there anything else I should know about woodworking?
Furniture making is a laborious task. It's easy not to appreciate how hard it is. The hardest part of the process is actually finding the right wood. There are so many wood options that it can be difficult to choose the right one.
Another problem is the fact that not all wood has the same properties. Woods can warp, split, or crack over time. You must take these things into consideration before purchasing wood.
Statistics
- Woodworkers on the lower end of that spectrum, the bottom 10% to be exact, make roughly $24,000 a year, while the top 10% makes $108,000. (zippia.com)
- Most woodworkers agree that lumber moisture needs to be under 10% for building furniture. (woodandshop.com)
- Average lumber prices rose about 600 percent between April 2020 and May 2021. (familyhandyman.com)
- In 2014, there were just over 237,000 jobs for all woodworkers, with other wood product manufacturing employing 23 percent; wood kitchen cabinets and countertop manufacturing employing 21 percent. (theartcareerproject.com)
External Links
How To
How to make wood joints
This tutorial will help you join two pieces of wooden together. We'll use the "pocket hole joint," which means we drill holes in the wood and then glue them together. If your wood has a straight grain, smooth surface, you can use this method. You might consider dowel joinery if your wood isn’t straight or flat. Here are the steps
-
Drill Pocket Hole Joints. Measure and mark the location where you would like to place the pocket hole joint. Use a jigsaw or handheld drilling machine to drill 3/8 inch deep holes at the ends of each wood piece.
-
Sand Smooth. You can sand the edges of the wood to ensure that it doesn't split.
-
Glue together. Apply glue to the sides of both wood. Let it sit for about 5 minutes before clamping the pieces together.
-
Secure the pieces together. After the glue has dried thoroughly, secure the pieces so that they are flush.
-
Trim Joinery. Trim the excess wood around the joint after the glue has dried completely.
Be sure to leave enough space between each piece so that they can be turned inside-out.