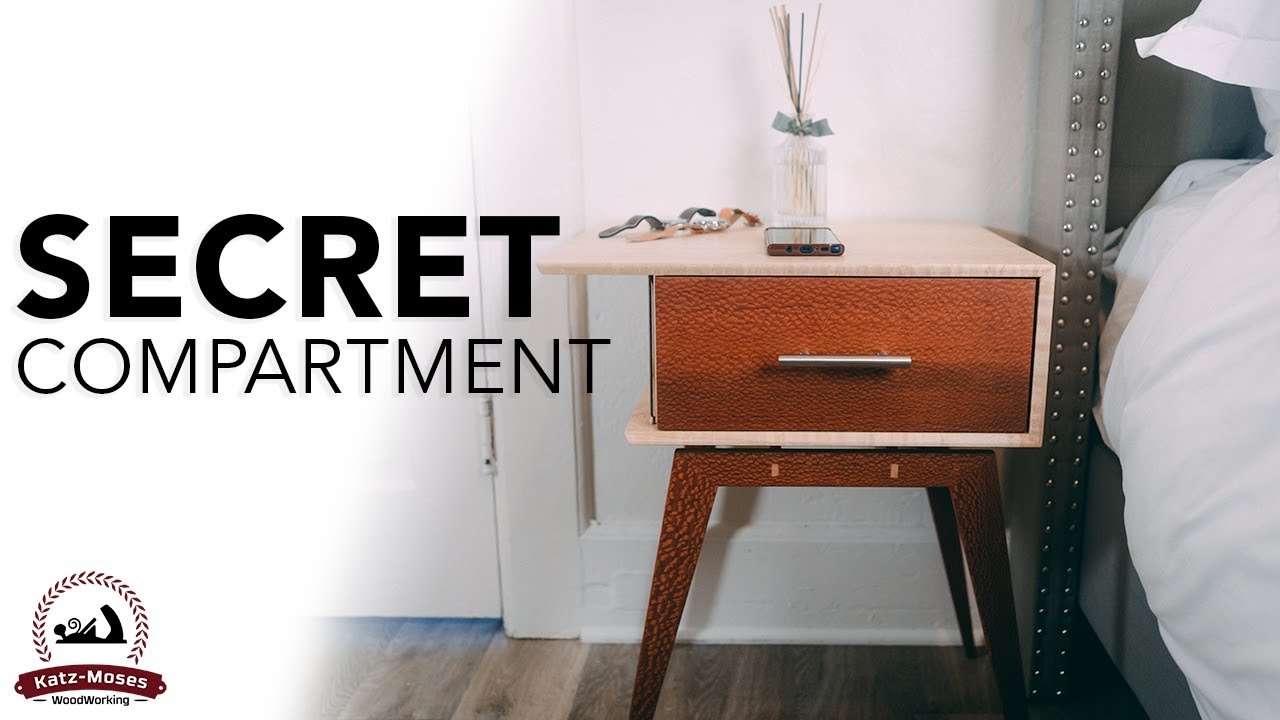
It can be difficult cutting rough lumber and loading it into your car is not easy. Be sure to take your hand saw and tape measure with you when you go to the store. Additional boards can be purchased in case the one you have bought doesn't fit. Make sure you have the right knots and checks on your board. Otherwise, they might not fit as well as you would like. You don't want to have to rip a board and start all over. It's a waste of time and money to do this, so you can buy one or two additional boards.
We save money!
A sawmill can turn 59% to 50% of rough lumber into boards by cutting it. The rest of a log is usually waste: sawdust chips, bark and chips. Even though a poor cut may result in more wasted wood, the amount should not exceed 20%. Here's a simple formula to estimate the amount of wasted wood in a board. For a nominal 4-foot board, the sawmill should remove about 18% of its volume to achieve the desired lumber thickness and width.
Rough lumber is not always available in standard dimensions. The dimensions of hardwood that you purchase from a big box retailer are often known. This allows for you to plan your project using the standard size. Rough lumber's edges don't always match up perfectly, causing waste. Furthermore, rough-cut lumber usually requires a common width, which causes a lot of wasted lumber. This waste cannot be reused later.
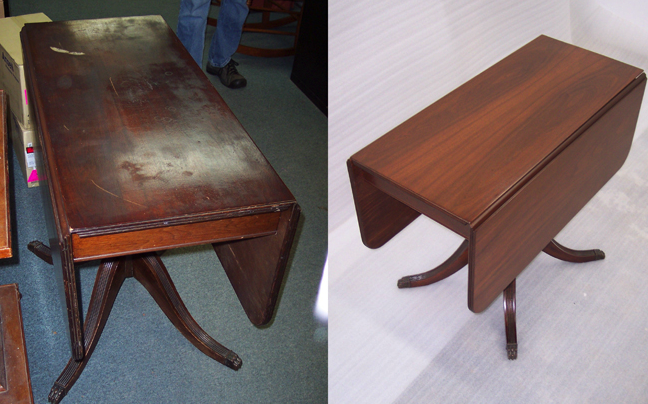
Preparation
The first step in preparing for cutting rough lumber is to measure the length of the material. The lumber yard may not have the rough lumber perfectly flat upon arrival. It may also not have parallel faces and edges, and may require several passes to flatten. A good rule of thumb is to remove 1/16" per pass. If your lumber has concave sides, it is best to run it through the circular saw with the concave edge down.
The rough cut lumber should generally be flattened to 1/4" before the saw cuts. After flattening, plane the face to the thickness you want for the finished board. Once you know the thickness of the rough lumber measure the finished length and width. You should account for any imperfections. Be sure to leave a minimum of one-quarter inch space on each side of the board. You can also plan your project using the available boards. Make sure the lumber you buy is flat enough, as rough boards that are warped, bowed, or twisted are difficult to work with.
Cost
There are two types, dimensional lumber and rough sawn lumber. Generally, home improvement stores carry finished lumber but rarely rough-sawn lumber. Both types of lumber are typically carried by local sawmills or lumber yards. The only difference between these two types lies in the work involved. Because it takes less work to make, rough-sawn boards are more affordable. It is also thinner and wider than finished lumber.
While buying lumber from a yard or mill is cheaper, you are less likely than others to find it in standard lengths. Making your own lumber can save you money over buying rough-sawn lumber. However it will require some space and additional power. Milling equipment can be noisy and requires training. You might want to check the zoning laws for your area before you start using your mill.
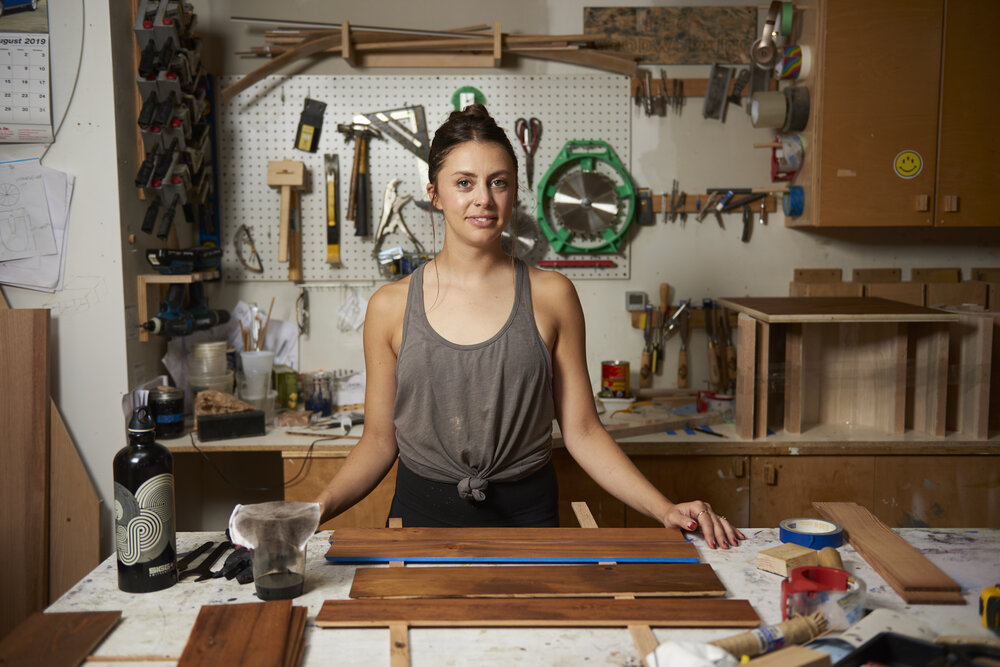
Source
There are many options for lumber purchases. There are many options for sizes, shapes, cut, and finishes. Rough sawn lumber, for example, is unsanded and unfinished lumber that has been cut into planks. This type of lumber is more durable than others because it contains more moisture. It's also thicker and stronger than surfaced wood. The following are some benefits of using rough sawn lumber for your woodworking projects.
First, it is affordable and readily available. Rough lumber isn’t treated and is not typically sold at a hardware retailer. However, this type lumber comes with its own pros and cons. Although it is less expensive per board foot, it is more expensive to transport. This wood takes longer to finish than the treated wood. You might also consider this option when deciding how much lumber you should purchase. For projects that will require rough sawn lumber, you might want to purchase a large amount and some for finishing.
FAQ
How often do I need to buy new supplies
Over time, you may need to replace your tools. Sharpening hand tools is a must. You'll also need to replace parts if you use power tools. Spread your purchases over several months to avoid purchasing too many items at once.
How much should a woodworker charge per hour?
The hourly rate paid to a professional woodworker is dependent on many factors. These include skill level, availability, and location.
A skilled woodworker can expect an hourly rate of $20-50.
A less experienced woodworker may charge as little as $10 an hour.
What's the difference?
Hobbyists love making things from wood while professionals are more concerned with the quality of their work. Hobbyists tend to take pride and share their creations with family and friends. Professionals will spend hours researching designs and then begin to create a project. Professionals will be meticulous about all aspects of their work, from selecting the right materials to finishing it.
Statistics
- In 2014, there were just over 237,000 jobs for all woodworkers, with other wood product manufacturing employing 23 percent; wood kitchen cabinets and countertop manufacturing employing 21 percent. (theartcareerproject.com)
- The best-paid 10 percent make $76,000, while the lowest-paid 10 percent make $34,000. (zippia.com)
- Woodworkers on the lower end of that spectrum, the bottom 10% to be exact, make roughly $24,000 a year, while the top 10% makes $108,000. (zippia.com)
- Most woodworkers agree that lumber moisture needs to be under 10% for building furniture. (woodandshop.com)
External Links
How To
How to join wood with no nails
Woodworking is a hobby that many people enjoy doing. Woodworking can be a fun hobby because you can work with your hands to make useful objects from wood. You may need to join two pieces without the use of nails. This article will demonstrate how to do so to preserve the beauty of your woodwork.
Before joining the pieces of wood together, you will need to first trim any edges. You don't want any sharp corners to cause problems later. Now it's time to start glueing your boards together.
If you are working with hardwood, only one side should be glue. If you are using softwoods such pine or cedar, glue should only be applied to one side. Apply the glue to the boards and press them down until they are securely attached. Be sure to let the glue dry before you move on to the next step.
After you've glued your boards, you'll want to drill holes into the joints where you plan to insert screws. Depending on what type screw you choose, the size of these holes will depend on how big they are. If you are going to use a half-inch wood screw, you will need to drill at least 3/4 inch deep.
After drilling the holes, you can drive the screws into your board's backside. Be careful not to hit the front surface of the board, or else you'll ruin the finish. Don't drive the screws too far into the end. This will prevent splitting in the end grain of the wood.
Once your project is complete, it's time to protect it against the elements. To do this, you can seal the entire furniture piece or just cover the top. It doesn't matter what method you use, you want something that will last many years. Some examples include oil-based varnishes, polyurethane, shellac, lacquer, etc.
These products can generally be found in any home improvement shop. Just make sure that you buy the right kind for the job. Keep in mind that certain finishes can be toxic and should not be used indoors. So, always wear protective gear when handling them.