
You may wonder, "Why would I need a tip to burn wood?" After all, a transfer tip will be the only thing between you and the surface that you want to burn. A wood-burning transfer tip can be found on many products, including portable stands that can hold it. Be sure to understand how to attach a tip to a wood burning torch and how it works.
Carbon paper
Use carbon paper to make a wood burning transfer tip. Make sure you prepare your pattern paper beforehand. The first step is to fold the pattern paper in half. Next, use the soft lead pencil to rub the entire design area. After you have completed the transfer, you can remove the carbon paper and redraw your design. You can also trace your lines with an ink pen. The ink can leave a trace when it burns, so ensure you follow your pattern exactly.
While most buyers report that using carbon paper is convenient, some found it difficult to use properly. Many prefer to use trace paper. This works well but it is important to not burn the paper to stop it from tearing. Carbon paper is good for wood burning and can be used again. Besides, it can save both time and paper. Carbon paper can also be used for many other purposes. Carbon paper can often be found in zip-lock bags.
Photo paper
You may feel tempted to burn the entire image when you are burning a photograph. It's tempting to just burn the entire photo. However, mirroring the image will ensure that the text will print correctly. Also, don't touch the glossy side of the photo because it can smear the ink. If you want to transfer a more detailed photo, you can use a chartpak colorless blender pen. This pen costs $5 and is great for transfer of lines and detailed images.
Photo paper is a great way to transfer patterns onto a smaller canvas. Photo paper is easy and convenient. It also avoids messy carbon papers. It is important to choose a photo paper that is smooth so it doesn't absorb ink from the printer. To transfer the image, place it on top of the wood.
Razertip Transfer Shader Pyrography
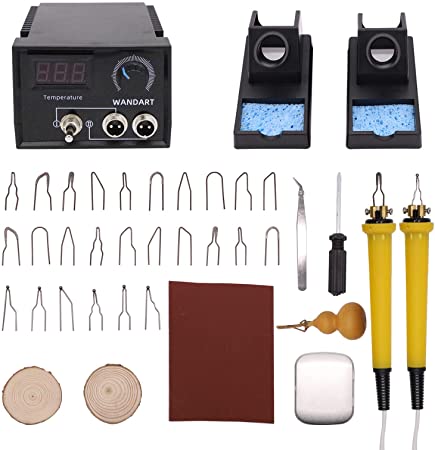
The Razertip Transfer Shader is one of the most popular wood burning tips available. The stainless steel tip with a teardrop shape is great for shading or transferring heat-photocopied images. To fit different projects, you can choose from three types of handpieces. Razertip pyrography tools can also be used to create fine lines. For more information, visit razertip.com.
Razertip pyrography pens are covered by a 1-year warranty. There are many tip types available. They are among the most compact pens on the market today. This makes them ideal for delicate detail work. They are made to last. Heavy-duty models are more durable and have larger pen bodies and thicker tips and connector posts. These models also require a higher heating temperature and a longer cord.
Graphite pencil
A tracing paper is one of the most important things you need when using a graphite tip for wood burning transfer. This paper will guide you in transferring your design from paper to wooden. You must first decide what design you want to transfer in order to make the transfer process as simple as possible. You can choose between a simple and more complex design, depending on the design. You may need to print the design before you transfer it.
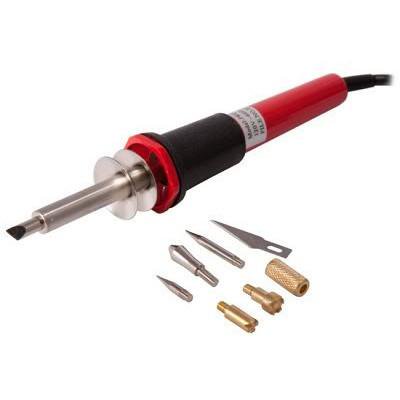
Place the graphite on the side that faces the wood. Follow the design lines with light to medium pressure. Once you've finished this process, take the paper off. You are now ready to transfer your design. An alternative method for beginners is to trace the design on paper by hand. However, this method won't work as well as a graphite pencil as it will cause the wood become stiffer.
FAQ
How much money does a hobbyist have to put into getting started?
A lot of capital is required to purchase the necessary supplies and tools if you want to start your own woodworking shop. You can start by purchasing a small table saw and drill press as well as a circular saw, circular saw, jigsaw and sanding machines. These items won't break the budget and aren't expensive.
Do you have any suggestions for starting a woodworking shop?
It takes a lot of effort to start a woodworking business. However, if you are passionate about your hobby you will be willing to put in the effort. You will probably love the challenge of starting your own business.
One thing to keep in mind when launching a new venture is that you might encounter unexpected problems along the way. For instance, you might run out of money unexpectedly. You might find customers not willing to pay the amount you expected. Preparedness is key to survival in such situations.
It is a good idea to create a separate bank account just for your company. You will always know how much money you have coming in.
What type of wood should I choose?
The most commonly used woods for woodworking are oak, maple, cherry. Each wood type has its own characteristics which affect the final product's appearance and feel. For example, oak tends to be darker and harder than other woods. Birch is lightweight and soft while mahogany is heavier and denser. You can also pick between veneers and solid wood. Veneers are thin sheets or wood that are glued together into one layer.
How can a novice woodworker make it big?
Many people are looking to create their own furniture and start an internet business. If you are just starting to build furniture, there are many other ways to make money than selling on Etsy. Local craft fairs and events are great places to sell your products. Or you could offer workshops for others who want to learn how to build their own furniture. If you have experience as a carpenter or builder, you might consider offering services such as remodeling homes or creating custom pieces for clients.
How often should I buy new supplies?
You will likely need to replace some tools over time. You'll need to sharpen your hand tools regularly if you use them. For power tools, replacement parts will be required frequently. To avoid buying too much at once, try to spread your purchases out over a few months.
How do I know what type of wood I'm dealing with?
Always check the label before purchasing wood. It should have information about the wood species as well its moisture content and whether any preservatives were used.
Statistics
- In 2014, there were just over 237,000 jobs for all woodworkers, with other wood product manufacturing employing 23 percent; wood kitchen cabinets and countertop manufacturing employing 21 percent. (theartcareerproject.com)
- Most woodworkers agree that lumber moisture needs to be under 10% for building furniture. (woodandshop.com)
- Woodworkers on the lower end of that spectrum, the bottom 10% to be exact, make roughly $24,000 a year, while the top 10% makes $108,000. (zippia.com)
- The best-paid 10 percent make $76,000, while the lowest-paid 10 percent make $34,000. (zippia.com)
External Links
How To
Tips for driving a nail in wood
When driving a nail into wood, it is important to first choose the correct size and kind of hammer. The most common types of hammers are claw hammers, sledgehammers, mallets, ball peen hammers, and hatchets. Each type of tool has its advantages and drawbacks. A clawhammer works best when hitting something hard like nails. However, it can sometimes be difficult to see exactly where the strike is going. The sledgehammer works well for large areas, but is too heavy for smaller tasks.
Place your hand flat on the side of your chosen hammer so that the handle rests in your palm. Grip the handle firmly, but don't squeeze it so tightly that you hurt yourself. Your wrist should be relaxed while you hold the hammer straight upwards. Swing the hammer back towards the ground, with your aim at the middle of the nail. You should feel the impact on the nail from the hammer. Try swinging a hammer using a block wood to practice until you are comfortable.
The hammer should be held close to your body when you are ready to begin driving the nail. To ensure that the nail is perpendicular on the surface of the wooden floor, position it. Keep your focus on the tip of each nail. Then, swing the hammer forward. Next, follow the motion of your hammerhead. This can be repeated several times to increase the speed of your swing. When you are confident with the technique, add power to your swings. Then, raise the hammer from your shoulder to bring it down. This will help you put more energy behind each of your moves.
Once you have made the first hole, remove your hammer. To pull out the remaining nails, use a screwdriver or pry bar. To avoid splitting the wood, make sure the nail heads are not touching the board's surface.